Rozpoczęcie produkcji centralnych komponentów nowego eActrosa 600 w zakładach Gaggenau i Kassel
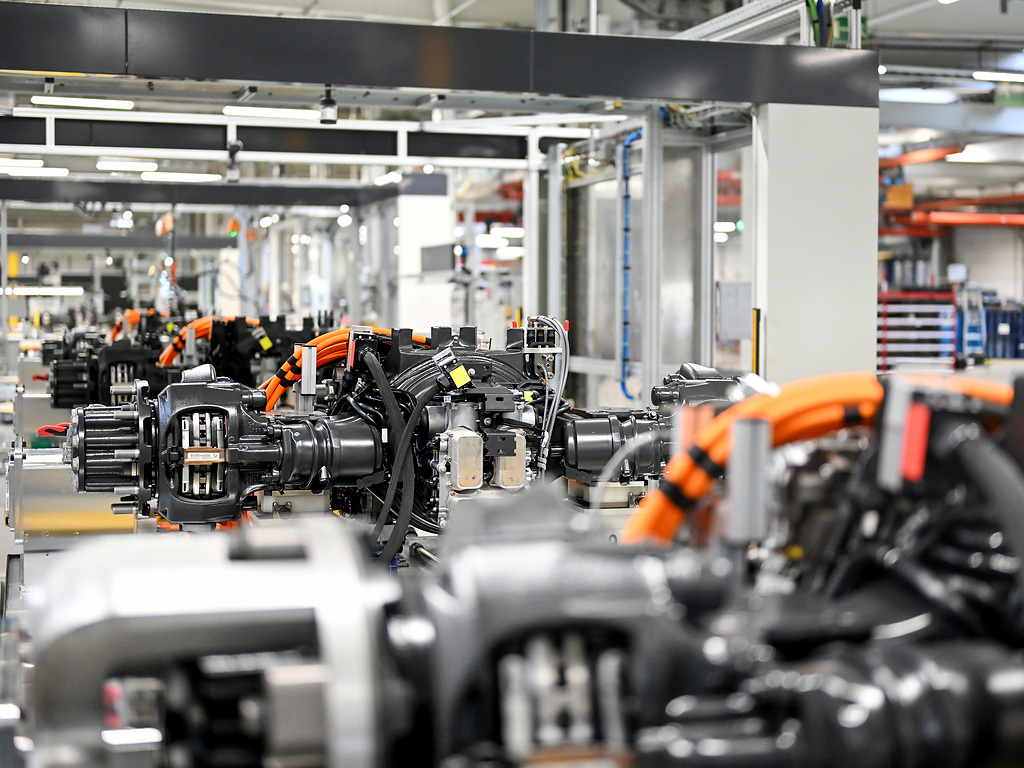
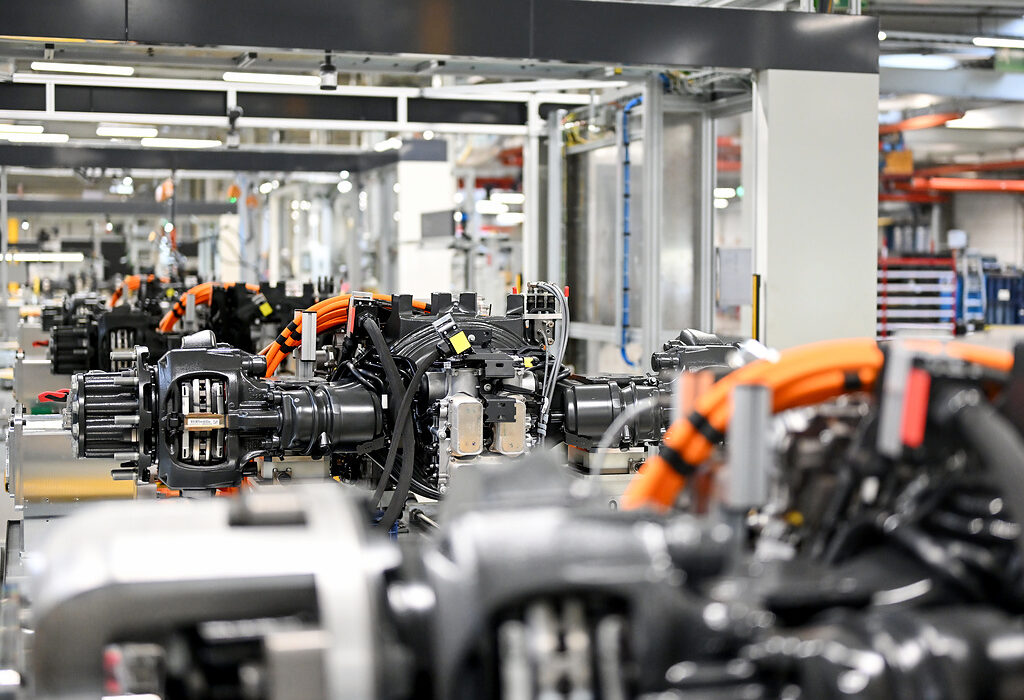
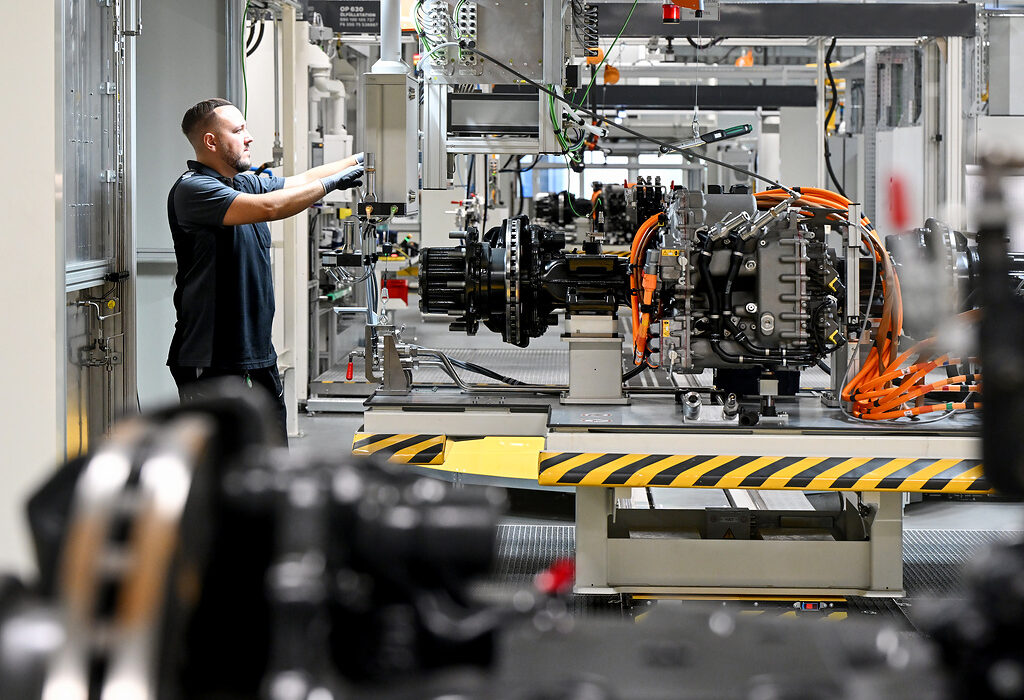
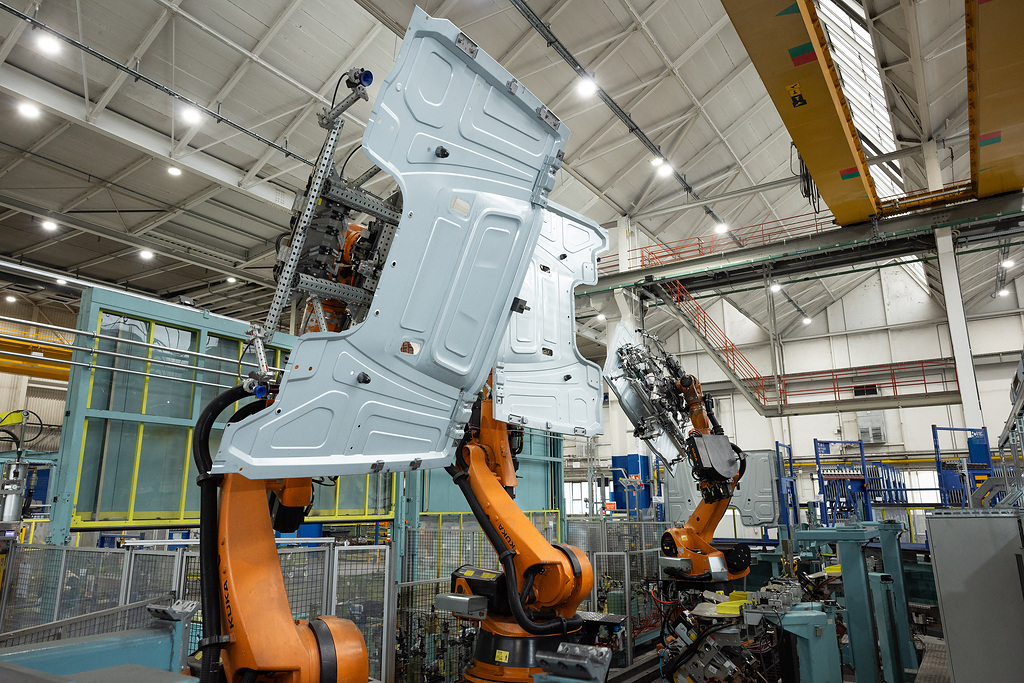

Pod koniec listopada 2024 roku Mercedes-Benz Trucks będzie świętować rozpoczęcie seryjnej produkcji eActrosa 600 w zakładzie w Wörth. Na targach IAA-Transportation w Hanowerze eActros 600 został niedawno wybrany „Międzynarodową Ciężarówką Roku 2025”. Pierwsze te pojazdy dla klientów zostaną wyprodukowane i zarejestrowane przed końcem 2024 roku. Kluczowe komponenty z zakładów Mercedes-Benz w Gaggenau i Kassel będą zamontowane w każdym aucie.
Kluczowe komponenty pochodzą z Gaggenau
Zakład Mercedes-Benz w Gaggenau, specjalizujący się w przekładniach do ciężkich pojazdów użytkowych, rozwija się obecnie w centrum wiedzy specjalistycznej w zakresie komponentów napędu elektrycznego. Od 2021 roku kluczowe części e-osi (jednostki łączącej oś, silnik i przekładnię, która stanowi elektryczny układ napędowy) eActrosa 300/400 do transportu dystrybucyjnego i eEconic są produkowane w Gaggenau. To samo dotyczy centralnych komponentów nowej generacji osi elektrycznej, która będzie napędzać eActrosa 600. Są to części mechaniczne, takie jak te, które Gaggenau od wielu lat produkuje do pojazdów z konwencjonalnymi układami napędowymi. Są one wykorzystywane do produkcji najnowocześniejszego, innowacyjnego 4-biegowego napędu osi, zawierającego łącznie około 30 różnych komponentów. Należą do nich specjalnie opracowane komponenty przekładni, takie jak wały, koła zębate i części synchronizatorów oraz części obudowy. Gaggenau dostarcza te komponenty do Kassel, gdzie odbywa się kompletny montaż osi i elementów przekładni, oraz powstaje nowo opracowana, elektrycznie napędzana oś tylna. Ponadto w Gaggenau są wytwarzane elementy poszycia i struktury nośnej kabin eActrosa 600. Zakres dostawy obejmuje między innymi elementy konstrukcyjne, takie jak tylny panel, rama dachu, grodź i belki poprzeczne, oraz różne wzmocnienia. Są to części przeniesione, już stosowane w ciężarówkach z napędem konwencjonalnym. Wiedza specjalistyczna zakładu w zakresie nadwozi „niesie” zatem zewnętrzną powłokę nowo zaprojektowanej kabiny nowego dalekobieżnego samochodu z napędem akumulatorowym.
Wszystkie elementy elektrycznego układu napędowego podlegają surowym wymaganiom pod względem jakości, żywotności i przestrzeni montażowej. Na przykład specyfikacje geometryczne powierzchni i chropowatości uzębienia kół zębatych i wałów dopuszczają jedynie bardzo wąskie tolerancje. Najnowsze i wysoce precyzyjne technologie produkcyjne, takie jak specjalistyczne szlifierki do kół zębatych, umożliwiają zagwarantowanie wymaganej jakości. Obróbka mechaniczna części obudowy odbywa się w specjalnie przebudowanej hali w fabryce w Gaggenau. Tutaj utworzono całkowicie nowy zakład wytwórczy z automatycznymi centrami przetwarzania. Podczas fazy zamówień wirtualne uruchomienie tych centrów umożliwiło symulację przetwarzania na tzw. „cyfrowych bliźniakach”. Proces ten zapewnia ogromne oszczędności czasu w porównaniu z konwencjonalnym procesem konfiguracji zakładu produkcyjnego. Obróbka mechaniczna obejmuje wiercenie i frezowanie oraz gwintowanie, zanim obudowy zostaną poddane testowi szczelności. Thomas Twork, kierownik zakładu Mercedes-Benz Plant Gaggenau, wskazuje „Nie ma przyszłości bez przeszłości! W zakładzie Mercedes-Benz w Gaggenau tradycja i transformacja idą ręka w rękę. Jesteśmy dumni, że w nowym elektrycznym układzie napędowym możemy wykorzystać nasze dziesięciolecia doświadczenia w produkcji wysoce precyzyjnych komponentów przekładniowych. Wspólnie z naszymi kolegami z zakładu montażowego w Kassel nasz zakład wnosi istotny wkład w bezemisyjną mobilność”. Michael Brecht, przewodniczący rady zakładowej koncernu Daimler Truck i przewodniczący rady zakładowej zakładu Mercedes-Benz w Gaggenau, dodał zaś „W szczególności wolumeny produkcji osi elektrycznej stanowią sieć produkcyjną z zakładem w Kassel. Wspólnie wnosimy znaczący wkład w nowy elektryczny układ napędowy. W ten sposób generujemy innowacje oraz dajemy pewność pracownikom, dzięki czemu możemy zająć się nowymi tematami technologicznymi”.
Nowo opracowana oś elektryczna jest rozwijana w Kassel
Zakład Mercedes-Benz w Kassel, koncernowe globalne tzw. centrum doskonałości w zakresie osi konwencjonalnych i elektrycznych układów napędowych, montuje nową generację osi elektrycznej dla eActrosa 600. Elektrycznie napędzana oś tylna została przeprojektowana specjalnie do transportu dalekobieżnego. Zawiera szereg innowacji technicznych zapewniających wyższą wydajność i efektywność. W tym celu w zakładzie zbudowano nową linię montażową, w tym stanowiska testowe i kontrolne dla funkcji związanych z bezpieczeństwem. Podobnie jak w przypadku osi elektrycznej obecnie stosowanej w modelach eActros 300/400 i eEconic, która jest już produkowana w Kassel, „zasada wspólnych części” obowiązuje także w przypadku nowej generacji. Oznacza to, że obudowa osi oraz elementy koła i układu hamulcowego pochodzą z konwencjonalnej osi, produkowanej przez zakład w Kassel od ponad dwóch dekad. Na linii montażowej elementy te powstają w bardzo elastyczny sposób, dzięki czemu zakład może zmieniać osie między konwencjonalnymi i elektrycznymi w zależności od sytuacji zamówienia.
Nowa generacja e-osi składa się z nadkola i elektrycznego układu napędowego obejmującego silniki elektryczne oraz elementy przekładni i wysokiego napięcia.
Proces montażu nowej generacji e-osi w Kassel
Całościowy proces montażu w zakładzie w Kassel odbywa się w różnych skoordynowanych fazach. Obudowa osi stanowi podstawę nowej e-osi i w pierwszym kroku jest przygotowywana do zawieszenia, toczenia i hamowania – tj. montuje się tutaj piasty kół, wały napędowe i bębny hamulcowe. Obudowa osi dla e-osi jest taka sama jak dla serii konwencjonalnej, dzięki czemu można ją łatwo dostosować do istniejącego podwozia pojazdu.
W obszarze montażu elektrycznego zespołu napędowego wstępnie zmontowane części przekładni, dwa silniki elektryczne i inne komponenty są instalowane w obudowie wspornika osi, która pochodzi z Gaggenau. W końcowym montażu odbywa się tak zwane połączenie wcześniej utworzonego elektrycznego zespołu napędowego z mostem osi. Ponadto różne czujniki, przewody olejowe i chłodzące oraz zestawy kabli niskiego napięcia są instalowane bez prądu.
Zanim elektryczna oś opuści zakład Mercedes-Benz w Kassel, w ostatniej fazie przechodzi szczegółowy test funkcjonalny komponentów mechanicznych i elektrycznych, tak zwany „test końcowy” (test EOL). To tutaj instalowane są kable wysokiego napięcia oraz są przeprowadzane próby szczelności i wysokiego napięcia. Na koniec elektryczna oś jest poddawana symulacji różnych sytuacji na drodze, w tym profili obciążenia, topografii i wyboru biegów. Po przejściu testu EOL, e-oś jest przygotowywana do transportu do zakładu Mercedes-Benz w Wörth.
Hauke Schuler, kierownik zakładu Mercedes-Benz w Kassel, ocenił „Jesteśmy dumni, że w naszym portfolio produktów mamy teraz też e-oś do neutralnego pod względem emisji CO2 transportu dalekobieżnego. Dzięki unikatowej i wydajnej konstrukcji, która integruje napęd elektryczny z istniejącą koncepcją osi, przyczynia się ona do dużego zasięgu eActrosa 600. To kolejny ważny kamień milowy dla zakładu Mercedes-Benz w Kassel w transformacji w kierunku mobilności bezemisyjnej”. Jörg Lorz, zastępca przewodniczącego rady zakładowej Daimler Truck i przewodniczący rady zakładowej Mercedes-Benz w Kassel, powiedzial z kolei „Nasz zespół w zakładzie Mercedes-Benz w Kassel jest pasjonatem produkcji nowej e-osi. W ten sposób wnosimy znaczący wkład w sukces tej innowacyjnej technologii napędu w Daimler Truck. Oba reprezentują wspólną sieć produkcyjną i technologiczną z zakładem w Gaggenau”.
O zakładach Mercedes-Benz w Gaggenau i Kassel
Zakład Mercedes-Benz w Gaggenau został założony w 1894 roku jako „Firma Bergmann’s Industriewerke in Gaggenau” i jest najstarszym zakładem motoryzacyjnym na świecie. Oprócz przekładni zakład produkuje osie planetarne i portalowe oraz komponenty aut osobowych, w tym przetworniki momentu obrotowego. Zakład w Gaggenau rozwija się obecnie w centrum kompetencyjne w zakresie komponentów napędu elektrycznego i montażu ogniw paliwowych na bazie wodoru. Wspólnie z Gehring Technologies GmbH zchce przyspieszyć prototypową konstrukcję tzw. silników elektrycznych „truck-e-fied” oraz dalszy rozwój i testowanie innowacyjnych procesów produkcyjnych. Zatrudniając około 4600 pracowników, jest największym pracodawcą w mieście i największą firmą szkoleniową w regionie. Kształcenie zawodowe ma także długą tradycję: od ponad 100 lat przeszło 10 000 młodych ludzi ukończyło naukę w najstarszym zakładzie motoryzacyjnym.
W zakładzie Mercedes-Benz w Kassel doświadczenie w produkcji ciężarówek sięga 1925 roku. Zakład ten został założony w 1969 roku jako „Hanomag-Henschel-
Tekst: Jarosław Brach
Zdjęcia: Producent