Rozpoczęcie produkcji centralnego komponentu eActros 600 w fabryce w Mannheim – to przednia część nadwozia

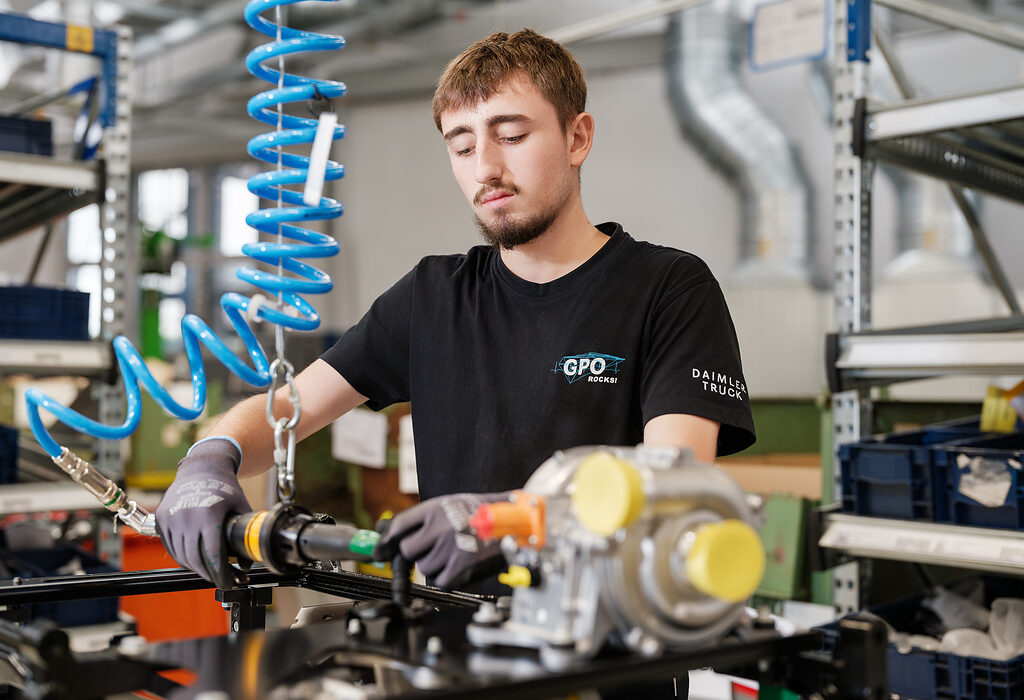

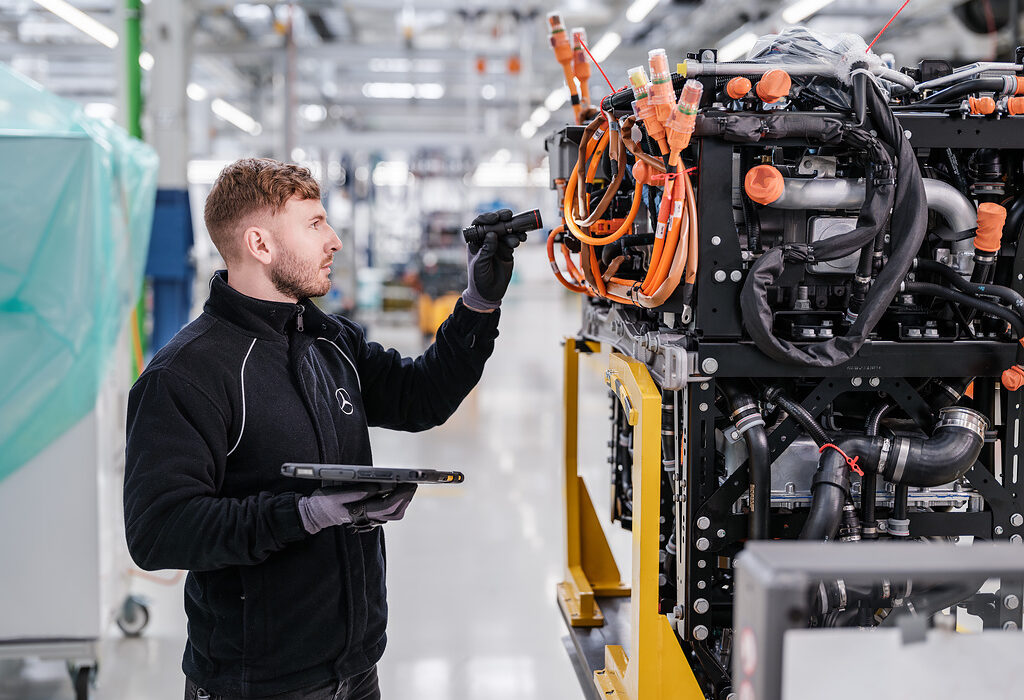
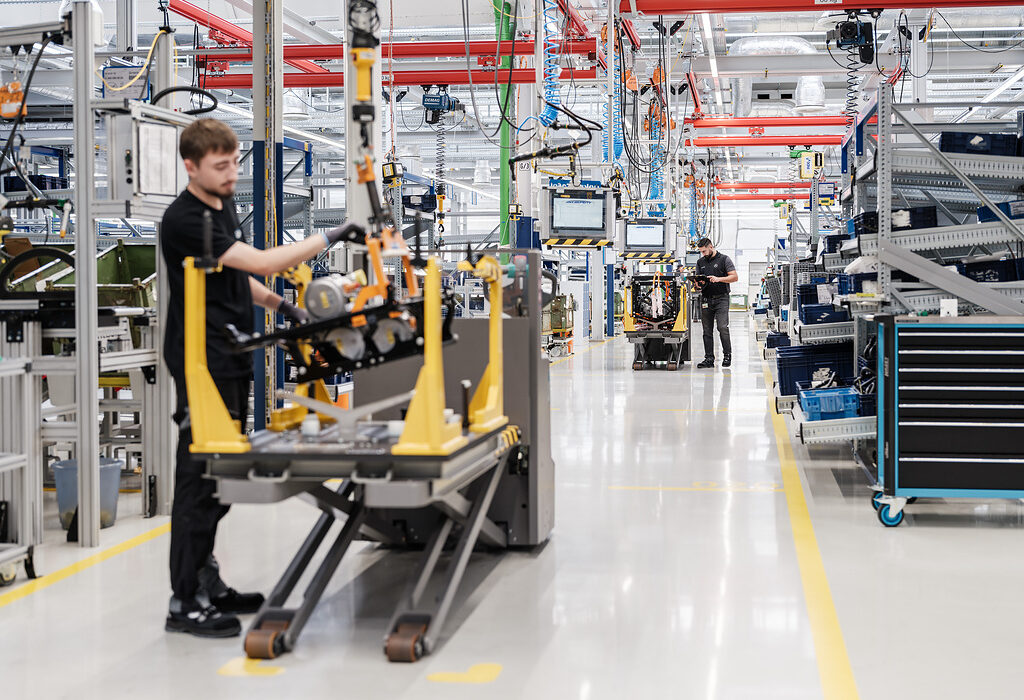
Pod koniec listopada tego roku Daimler Truck będzie świętował rozpoczęcie seryjnej produkcji w fabryce w Wörth akumulatorowo-elektrycznego wariantu do transportu dalekobieżnego Mercedes-Benz eActros 600. Oczekuje się, że pierwsze pojazdy dla klientów zostaną wyprodukowane i zarejestrowane w 2024 roku. W każdym pojeździe montowany będzie centralny podzespół z fabryki Mercedes-Benz w Mannheim: tzw. przednia skrzynia.
O przednim module
Moduł – skrzynka przednia to złożony moduł technologiczny z kilkoma urządzeniami sterującymi, komponentami wysokiego napięcia i elektryczną sprężarką powietrza, zlokalizowaną w dawnej przestrzeni montażowej silnika spalinowego. W przeciwieństwie do silnika wysokoprężnego, przednia skrzynia nie pełni określonej funkcji napędowej, ale zawiera szereg podzespołów niezbędnych do działania auta. W sumie jest to ponad 1000 pojedynczych części. Umieszczenie tak dużej liczby podzespołów na bardzo małej przestrzeni było szczególnym wyzwaniem w procesie opracowywania. Ostatecznie udało się to osiągnąć za pomocą tak zwanej „struktury poziomej”, w której poszczególne elementy są budowane od dołu do góry. Andreas Moch, kierownik budowy w fabryce Mercedes-Benz w Mannheim, wskazał „Przednia skrzynia to jednostka wymagająca intensywnego montażu w pojazdach zasilanych akumulatorowo. Po udanej fazie prototypu jesteśmy teraz zadowoleni, że możemy przejść do produkcji seryjnej. Zarówno przygotowanie ramy, jak i montaż wszystkich poszczególnych komponentów oraz testowanie tych zespołów przeprowadzane są w fabryce Mercedes-Benz w Mannheim. Nasza fabryka Mercedes-Benz w Mannheim w zakresie technologii akumulatorów i systemów wysokiego napięcia stanowi centrum kompetencyjne w Daimler Truck. Wraz z rozpoczęciem produkcji przedniej skrzynki, osiągamy już drugi kamień milowy w tym roku po uruchomieniu latem naszego Centrum Technologii Baterii. Uważamy, że jesteśmy dobrze pozycjonowani w tym miejscu w ramach transformacji i wnosimy istotny wkład w kształtowanie bezemisyjnej mobilności przyszłości”. Bruno Buschbacher, przewodniczący rady zakładowej fabryki Mercedes-Benz w Mannheim, ocenił „Jestem bardzo zadowolony, że pomyślnie wprowadziliśmy na rynek przednią skrzynię, pierwszy produkt w ramach porozumienia osiągniętego w 2021 roku, i że część alternatywnego układu napędowego jest teraz mieści się w Mannheim. To ważny krok w transformacji naszej tradycyjnej lokalizacji silników. Głębokość produkcji przyszłości musi w dalszym ciągu umożliwiać samodzielne wytwarzanie niezbędnych komponentów. Jeśli spojrzymy w przyszłość, niezwykle istotne jest dalsze inwestowanie w przyszłość produkcji silników oraz w nowe produkty i kwalifikacje pracowników, aby pomyślnie opanować tę transformację, a tym samym w dłuższej perspektywie zapewnić w Mannheim bezpieczne i atrakcyjne miejsca pracy „
Budowa linii produkcyjnej
Zakrojone na szeroką skalę prace remontowe mające na celu utworzenie linii do produkcji modułów czołowych trwały około roku w budynku, który ma ponad 100 lat. Na powierzchni około 5500 m² odnowiono między innymi wykładzinę podłogową, wentylację i oświetlenie hali oraz przebudowano konstrukcję nośną. Zainstalowano wówczas nowoczesną linię produkcyjną ze strefą logistyczną. Oferuje ona wysoki poziom elastyczności w przypadku różnych ilości, wariantów wyrobu i kolejnych generacji. Linia montażu skrzynek czołowych składa się z czterech kolejnych sekcji wytwórczych. W każdej z tych sekcji znajdują się różne stanowiska montażowe, przy których po bokach są odpowiednie strefy materiałowe i wstępne montaże. Tutaj poszczególne poziomy frontu kompletuje się jeden po drugim. Po każdym ukończonym poziomie front box przechodzi przez tzw. bramkę jakości, podczas której sprawdzane jest prawidłowe wykonanie procesu montażu przed ustawieniem kolejnego poziomu. Po pomyślnym przejściu wszystkich bramek jakości i potwierdzeniu jakości montażu w tak zwanym „teście końca linii” (test EOL), skrzynia czołowa jest przygotowywana do wysyłki do fabryki Mercedes-Benz w Wörth.
Kwalifikacja w nowym centrum szkoleniowym wysokiego napięcia w Mannheim
Dla monterów zatrudnionych przy produkcji przednich skrzyni motto brzmi: „Montaż to montaż” – choć nieco inaczej niż w przypadku konwencjonalnych silników Diesla. Zespół produkcyjny liczy obecnie 25 pracowników, ale w przyszłości może ich być nawet 170. Aby optymalnie przygotować pracowników fabryki w Mannheim na wyzwania transformacji, od października tego roku szkolą się oni. Oferuje im się praktyczne środowisko edukacyjne, w którym uczestnicy mogą kompleksowo poznać najnowsze technologie wysokiego napięcia i akumulatorów. Stosowane są innowacyjne metody nauczania, takie jak okulary wirtualnej rzeczywistości i technologia rozszerzonej rzeczywistości.
Inne kluczowe komponenty z Gaggenau i Kassel
Fabryki w Gaggenau i Kassel, będące częścią sieci produkcyjnej i technologicznej Daimler Truck zajmującej się komponentami napędu elektrycznego i systemami akumulatorów, będą również dostarczać komponenty centralne do eActrosa 600. Elementy przekładni, takie jak wały i koła, oraz części obudów, będą produkowane w fabryce Mercedes-Benz w Gaggenau, centrum kompetencyjnym komponentów napędów elektrycznych. Są one dostarczane do fabryki Mercedes-Benz w Kassel, centrum kompetencyjnego w zakresie konwencjonalnych osi i elektrycznych układów napędowych. Tutaj odbywa się kompletny montaż elementów osi i przekładni.
O eActrosie 600
Pod koniec 2023 roku swoją światową premierę miał eActros 600 do transportu dalekobieżnego. Wysoka pojemność akumulatora wynosząca ponad 600 kilowatogodzin [1] – stąd oznaczenie typu 600 – oraz opracowana własna nowa, szczególnie wydajna elektryczna oś napędowa, umożliwiają elektrycznym ciężarówkom zasięg 500 km bez ładowania pośredniego. Zasięg ten osiąga się w bardzo realistycznych, praktycznych warunkach przy całkowitej masie zestawu równej 40 ton i można go znacznie przekroczyć w zależności od stylu jazdy i trasy. eActros 600 będzie w stanie pokonywać nawet ponad 1000 kilometrów dziennie. Umożliwia to przerywane ładowanie podczas wymaganych prawem przerw dla kierowcy – nawet bez ładowania megawatowego – pod warunkiem dostępności opcji ładowania. Oprócz ładowania CCS z mocą do 400 kW eActros 600 będzie później umożliwiał ładowanie megawatowe (MCS).
O fabryce Mercedes-Benz w Mannheim
W 1908 roku w Mannheim-Waldhof nad Luzenbergiem powstała dzisiejsza fabryka Mercedes-Benz w Mannheim. Ponad 4600 pracowników produkuje w zakładzie silniki i powiązane komponenty do pojazdów użytkowych. Jest to też centrum kompetencyjne Daimler Truck w zakresie technologii akumulatorów i systemów wysokiego napięcia, które znacząco przyczynia się do seryjnej produkcji portfolio produktów zelektryfikowanych. W tzw. Centrum Technologii Baterii zlokalizowano osobną linię pilotażową do produkcji prototypów ogniw akumulatorowych. Rozwój w tym przypadku dotyczy opracowywania koncepcji montażu i systemów akumulatorów. Odlewnia zakładu jest jednym z wiodących na świecie producentów żeliwnych odlewów samochodowych. W tzw. europejskim centrum produkcji silników zamiennych przygotowywane są także silniki do pojazdów użytkowych i aut osobowych.
W Mannheim znajduje się również fabryka Daimler Buses. To centrum kompetencyjne w zakresie autobusów miejskich wszystkich typów napędu i część sieci produkcyjnej Daimler Buses. Z linii wytwórczej na miejscu zjeżdżają między innymi w pełni elektryczny autobus miejski eCitaro oraz eCitaro z ogniwem wodorowym, zwiększającym zasięg. Od 2024 roku fabryka przystosowana jest do produkcji w 100% elektrycznych autobusów miejskich
Poza tym kształcenie i zabezpieczanie młodych talentów okazuje się równie ważne dla lokalizacji w Mannheim: dzięki ponad 100-letniemu doświadczeniu młodzi ludzie są szkoleni w tej lokalizacji – łącznie ponad 11 000 młodych ludzi ukończyło tutaj swoje szkolenia.
[1] eActros 600 jest wyposażony w trzy zestawy akumulatorów, każdy o mocy 207 kWh. Oferują one łączną moc zainstalowaną wynoszącą 621 kWh. Nominalna pojemność nowego akumulatora, w oparciu o wewnętrznie określone warunki ramowe. Może się to różnić w zależności od zastosowania i warunków środowiskowych.
Tekst: Jarosław Brach
Zdjęcia: Producent